How to deal with the defects of the casting hammer
2021-03-08
How to deal with the defects of the casting hammer
Pores are a common defect in hammers. There are usually two kinds of pores: one is spherical bubbles with different sizes on the inner and outer surfaces of the hammer head,
which are characterized by the smooth inner wall of the pores alone or clustered together; the other is the small honeycomb-shaped particles scattered inside the hammer head.
Pinhole. It is mostly concentrated in the thicker part of the hammer head, and the pores are relatively smooth.
We have listed the causes of stomata one by one.
①: The design of the pouring system of the hammer mold is incorrect, and the molten metal produces eddy currents and entraps gas.
②: The hammer mold has poor exhaust, and the gas cannot escape smoothly from the mold.
③: The sand core or shell core is poorly exhausted, the sand core or shell core is stained with moisture, and the gas is not exhausted.
④: The metal flow is uneven during pouring or the pouring is interrupted to bring in gas.
The method of preventing the generation of pores is as follows.
①: Improve the design of the gating system, such as changing top injection to bottom injection, and bottom injection to serpentine runner.
②: Clean the exhaust plug in the hammer mold: increase the exhaust duct of the mold.
③: Make necessary exhaust ducts on the sand core. At the same time, it should be ensured that these exhaust ducts can communicate with the outside atmosphere
after the sand core, shell core and hammer mold are assembled.
after the sand core, shell core and hammer mold are assembled.
④: The sand core should be dried, and the dry sand core and shell core should not be stained with water: After the metal coating is peeled off during the casting
process, it should be noted that the water on the paint completely evaporates.
process, it should be noted that the water on the paint completely evaporates.
⑤: The pouring should be uniform and not interrupted, so as not to bring in gas. In order to facilitate the exhaust of the mold, inclined pouring can be used.
⑥: Reasonably stipulate and strictly control the pouring temperature of the casting hammer.
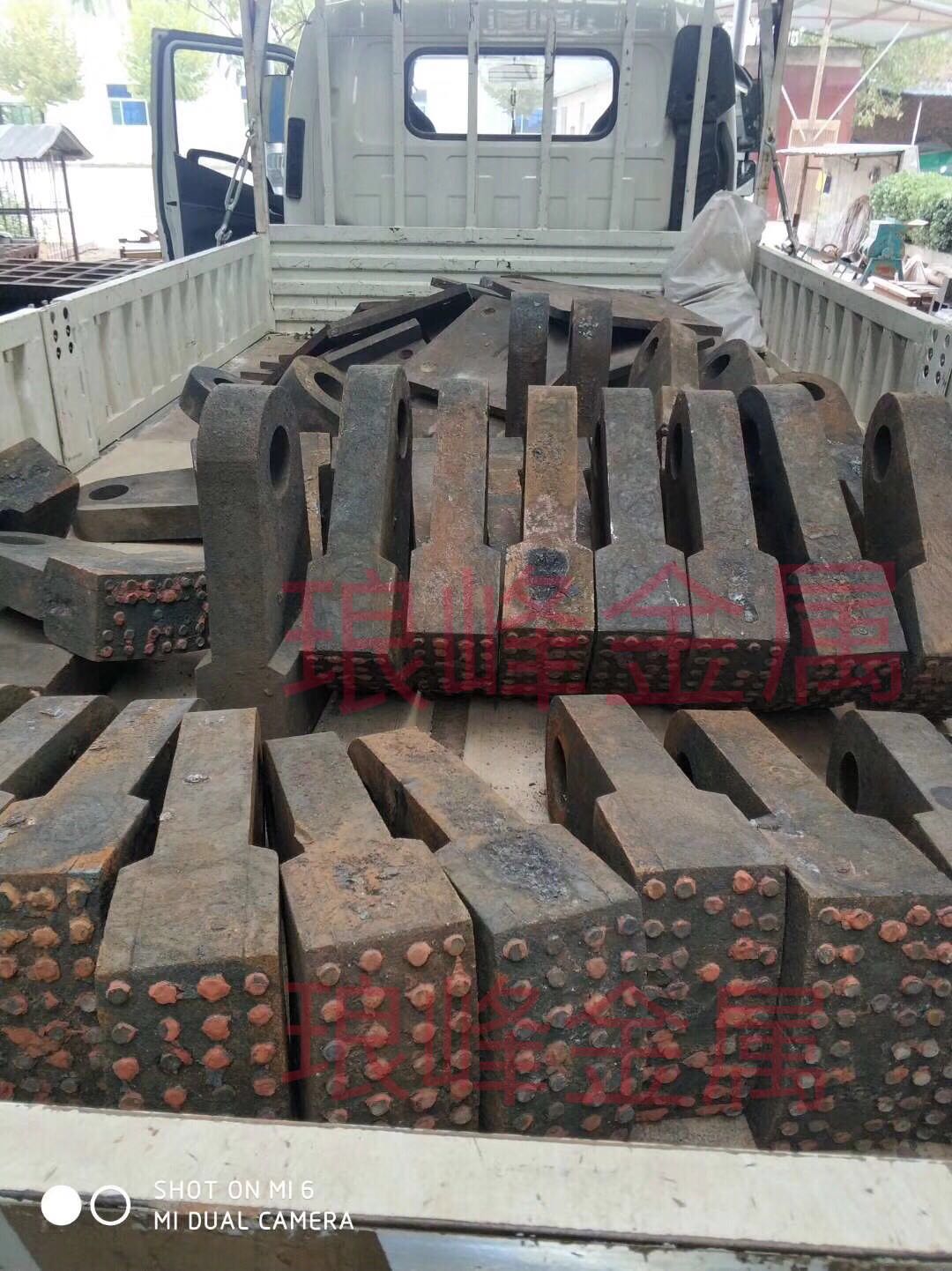
Registered with the Changsha Long-ping of High-tech Industrial Park in 2009, Hunan WISE New Material Technology Co.,Ltd, is a hi-tech private enterprise specialized in the development,production and sales of carbide powders, tic ferro alloys, wear resistant PTA hardfacing materials.
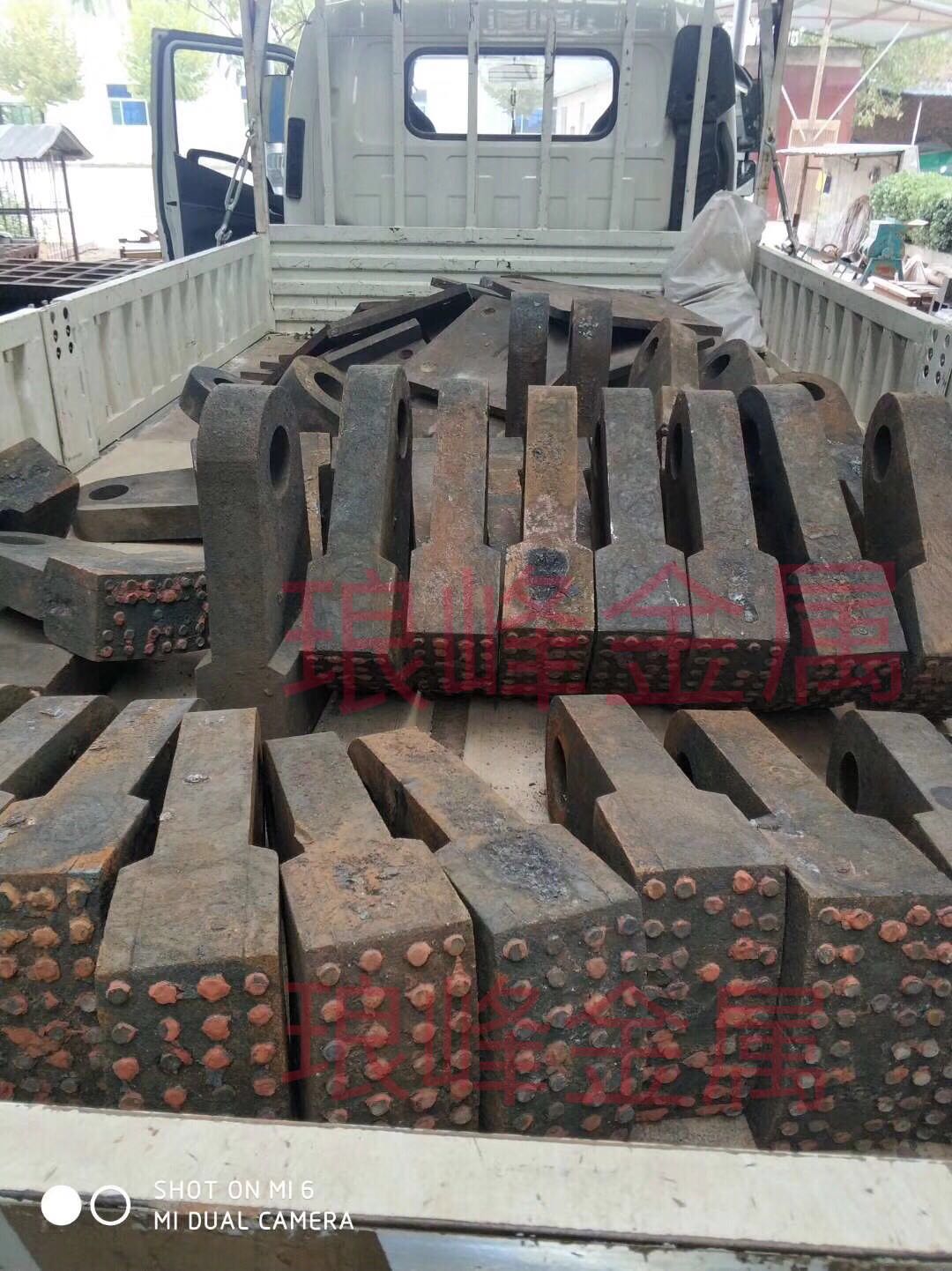
Registered with the Changsha Long-ping of High-tech Industrial Park in 2009, Hunan WISE New Material Technology Co.,Ltd, is a hi-tech private enterprise specialized in the development,production and sales of carbide powders, tic ferro alloys, wear resistant PTA hardfacing materials.