The conventional heat treatment
2016-03-07
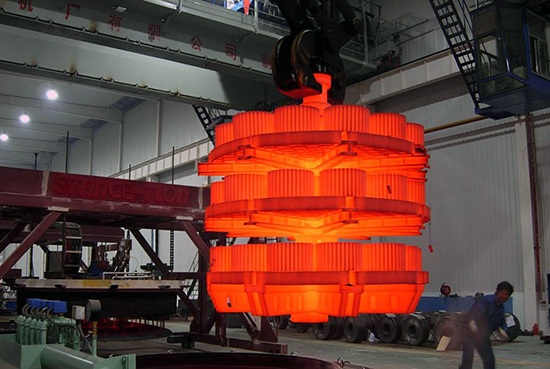
GJW50 mold material is used as a cold mold works well for hot die poor results, mainly due to thermal fatigue and early failure occurs. The test that the optimized heat treatment conditions, may improve the thermal(zirconium carbide) fatigue resistance of the steel matrix phase, thereby inhibiting or termination of thermal fatigue crack in the expansion phase of the steel substrate. Optimum heat treatment process is: 1050 ℃ quenching, 500 ℃ tempered.
Metallurgical microscope hot crack microstructure showed that: a sample of the treatment process, the expansion of the thermal fatigue crack reaches the steel substrate relative to the forefront not directly pass through the steel matrix phase, but Abduction Road to find other ways conducive to the expansion, thus increasing the steel matrix phase thermal fatigue resistance.
For strength, hardness and wear resistance are wearing parts can satisfy the mold and the requirements of the steel bonded carbide, try our best to improve its toughness is to further improve the goal of this material. Research GJW50 (ingredients % omega: 50 wc, 0.25 C and 0.50 more than 0.25 Mo, Cr, Fe) as the austenitic, 200 ℃, 1020 ℃ (below) Ms point after isothermal quenching of organization and mechanical properties showed that the state organization compared to + 1020 ℃ and 1020 ℃ quenching tempering state, residual austenite volume increased significantly; After isothermal quenching of HRC, sigma bb and alpha k values were significantly higher than that of tempered state, but significantly lower than the tempering state KIc value; 200 ℃ isothermal process, the residual austenite in due to a large number of epsilon carbide precipitation, and results in the formation of super fine isothermal martensite, is the main factor alloy strengthening; More in the tissues of the isothermal quenching residual austenite is alpha k value was significantly higher than that of the main reason for the quenching tempering state.
DGJW40 steel bonded carbide to adopt new technology, has a better organization and performance, its content by weight percentage of containing 40% WC, the rest is alloy steel, C content is 0. 6%, Mo, Cr content is about 2%. 880 ℃ 880 ℃ by 2 h + x 8 h annealing, quenching and tempering treatment by different process, the results show that the 1150 ℃ heating quenching + 150 ℃ x 3 h temper is the best process, can make the alloy to obtain excellent wear resistance.
With QRO90 high-quality hot-work die steel as matrix and WC as hard phase steel combined with gold, to quenching tempering process test showed that the quenching temperature has significant impact on the performance of alloy, alloy by 1000 ℃ quenching, 560 ℃ tempering, bending strength, hardness and impact toughness can be obtained the comprehensive performance of the alloy.
Stay tuned for detailed product information company official website:http://www.langfengmetallic.com/
Stay tuned for detailed product information company official website:http://www.langfengmetallic.com/