The main points of the metal powder flame spraying (welding) process (a)
2016-02-29
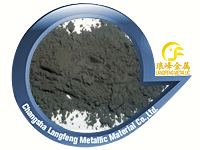
According to the author of this article is mainly engaged in thermal spraying twenty years of practical experience, for different workpiece material, coating selection, coating quality control and process points so play "initiate" role.
First, the process selection
1, to understand the performance of the workpiece itself: such material, composition, surface condition, wear parts and wear area and depth.
2, to understand the work conditions of use: Use the environment (temperature, major media concentration and other ingredients), the forces (impact load or sliding fit, interference fit), Failure (machining tolerance, wear, corrosion, etc.).
3, the following conditions should be used spraying:
1)surface by static load or low-speed sliding load, requiring abrasion resistant coating and the substrate but the tensile bond strength requirements do not exceed 50N / mm2 work-piece, spray layer hardness HV130-350, coating thickness from 0.3 to a few millimeters, spray state surface roughness Ra10-25μm, coating the surface roughness after grinding up Ra0.8-0.4μm, such as a variety of shaft bearing portion.
2) require resistance to cavitation erosion and processing after the surface roughness of not more than Ra0.4μm, such as imported cars crank, crank train, marine crankshaft.
3) made of a copper alloy, aluminum or aluminum and other nonferrous metals, the need to restore or increase the size of the surface abrasion resistance.
4) On the non-ferrous metal work-piece copper alloys, aluminum or aluminum alloy, such as spraying the best selection of copper-based powder or aluminum powder.
5) use in corrosive media, non-porous coating density requirements should be based on the work environment, operating temperature, media concentration and composition, selection can be used to meet the conditions of plastic, ceramic or corrosion resistant metal sprayed again with a suitable closure pore-forming agent to be closed coating process.
6) the bonding strength of the coating layer and the substrate: the traditional flame-sprayed layer tensile bond strength is generally 20-30N / mm2, the use of Shaanxi Branch Surface Engineering Co., Ltd. the latest development and production of multi-functional high-speed ZK8032 powder flame spray gun, in ductile cast iron sandblasted surface coating aluminum-clad nickel composite coating, the coating shear bond strength of up to 63.7N / mm2; high although not as good as spray coating layer, layer bond strength, but for repair work between the lubrication of metal friction resistance failure of parts is sufficient to meet the computing needs through research units, in Jiefang CA141 car loaded runs, seven of the crankshaft main journal shear stress concentrated on a spindle neck is also just 15N / mm2;. for 75 Dongfanghong tractors then only 5.5N / mm2, the shear strength of these data is far below the sprayed layer.
7) spray coatings wear: the automotive crankshaft spray, for example, spraying the crankshaft main journal and new compared to the higher wear resistance, once I sprayed in Japan Hino Motors crankshaft main journal repair overhaul after Check the abrasion of 0.022-0.03mm, the amount of wear and main journal without spraying repair of 0.2-0.25mm, which is almost a difference of ten times the amount of wear, from this example can illustrate sprayed layer has good abrasion resistance, even in lack of oil in case the engine still insist on running for several hours without axle bush-burning phenomenon.
8) Spray and spray technology differences:
① and combination spray layer and the base metal coating layer is formed of different nickel clad aluminum exothermic chemical reaction occurs when heated by the flame spraying bundle up in by sand-blasting Sa3 level, RZ> 50μm formed on the surface of carbon steel micro metallurgy Working in conjunction with the underlying layer and produce "anchors" effect of mechanical bond coating, and combined with spray layer and the substrate is purely metallurgical bonding coating.
② different coating materials, spray requires the use of self-fluxing alloy powder, and the coating is less demanding self-fluxing powders, and are not necessarily self-fluxing alloy powder, a variety of self-fluxing alloy powder used for both spray can be used for spraying, but spraying powder does not have the self-fluxing can not be used for spraying and spray process.
③ work-piece heating situation is different, and spray coating process, spray different preheat temperatures, different heat-affected parts, the organization of the work-piece, the performance is also different after spraying.
④ different dense coating, spray dense layer, but a small amount of porosity sprayed layer.
⑤ different load-bearing capacity, spray coatings are generally able to withstand large-area contact, more lubrication conditions at the work surface, with the face as well as other smaller force operating conditions using spray layer able to withstand greater impact force, compressive stress or exposure to stress.
Stay tuned for detailed product information company official website: http://www.langfengmetallic.com/
Stay tuned for detailed product information company official website: http://www.langfengmetallic.com/